Sawmill Design/Build – Part 26
Continuing with painting the main building interior parts but also...
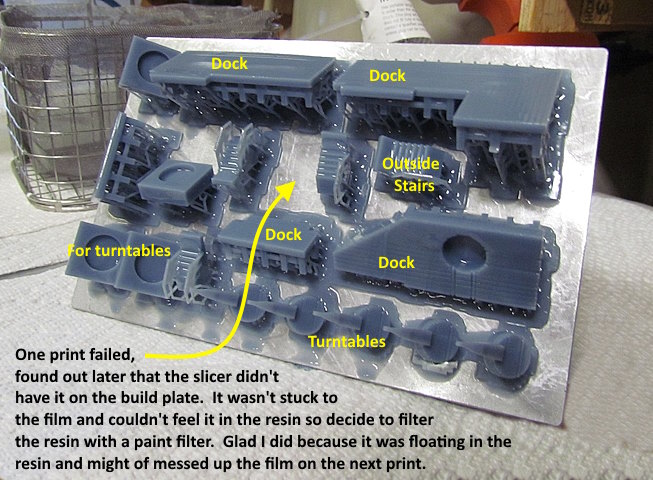
….. had to do a slight redesign of some of the exterior building detail. I’d raised the building a scale foot by putting a perimeter footing around it. That meant that I also had to raise all of the exterior docks and stairs a foot. Did that and then reprinted them. Slight problem when one of the prints didn’t print due to the fact it wasn’t on the build plate (probably my fault). It started printing up in the air off the plate so didn’t stick to the plate.
Presented some confusion as I couldn’t figure out where it went or what happened. Normally a failed print ends up stuck to the film on the bottom of the resin since they fail somewhere after the print starts. I ran my silicon spatula all around in the resin and on the film and couldn’t feel anything so almost went on to the next print. Glad I didn’t and took the time to filter the resin through a paint filter and found the failed part. If I would of gone on the build plate could of come down on the next print and pressed the failed print into the FEP film and maybe ruptured it. If you don’t have them maybe consider spending
under $10 for 100 paint filters.
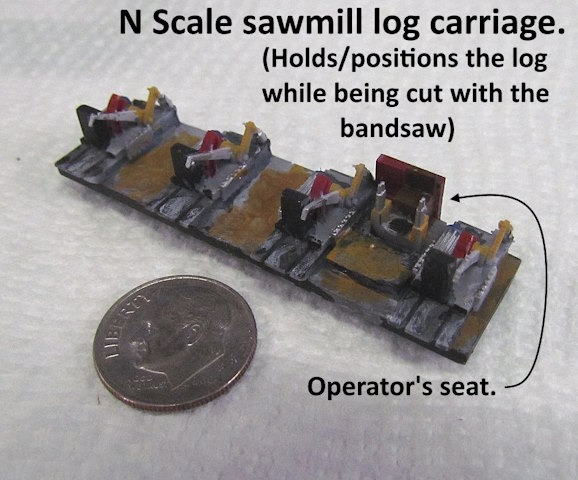
I’m using my smallest brush (very few fibers) and it works but these parts are really small and painting detail down to under .010” (.25mm) is challenging but I enjoy it and accept some errors. Also find that the more I do of this that it seems my 80+ year old hands shake less. I think it is having to relearn muscle memory that I’ve lost.
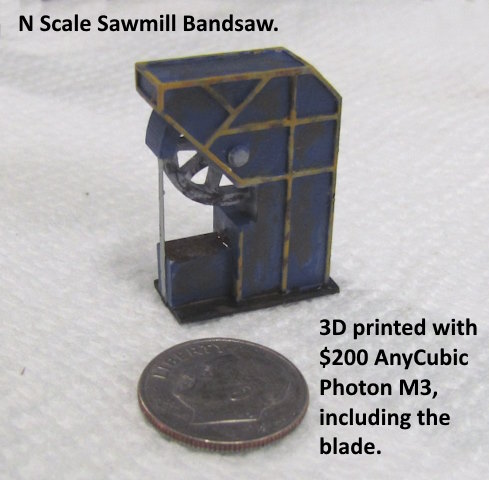
.
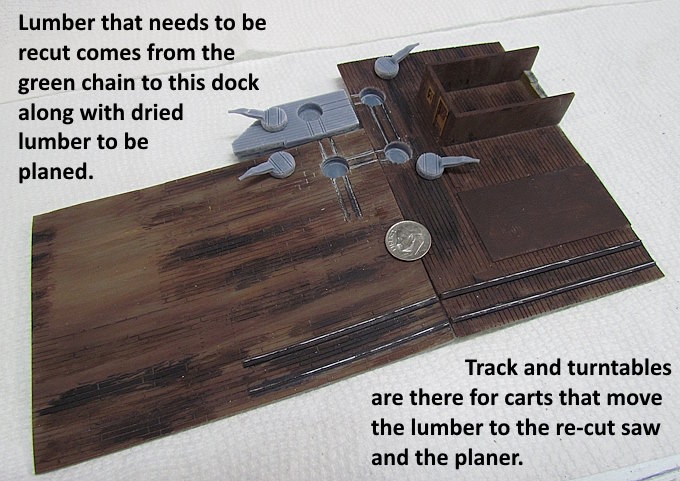
I hadn’t left the proper depth for the holes for the turntables above to rotate in so fixed the print that I’ll post the files for but didn’t want to reprint the two floors so cut the holes out and printed capture pieces that I glued under the floors for the turntables to sit in. The turntables are there to move carts with lumber loads into the mill from the dock just outside to the planer and re-cut saw.
The turntables allow for more than one cart to be involved as an empty cart can continue around the track and back to the dock without interfering with another cart. They are turned by hand.
The Hull-Oakes mill who I used to some degree for this project doesn’t have them I did see on another HO scale mill where carts were used somewhat like this to move loads out of the mill to either be dried, shipped or planed. I thought this added more interest to the mill but have no idea if it has ever been used like this (my mill, my mill plan is/was my plan).
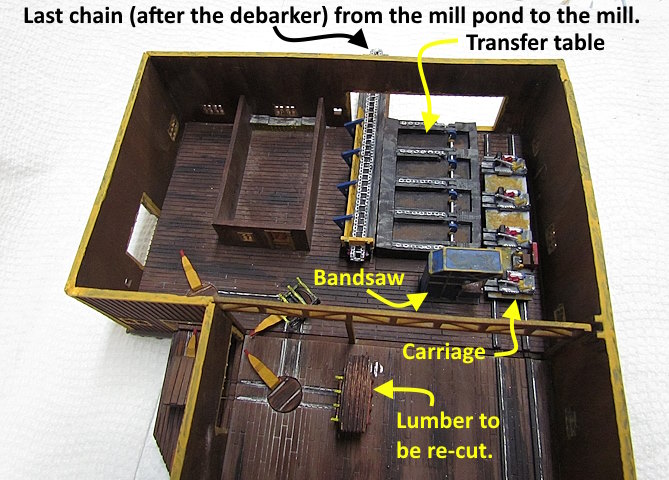
I painted all the equipment needed to get the log in and cut into a slab. The chain in, transfer table, log carriage and bandsaw are show above.
Next up is painting the printed parts shown above that are still grey.
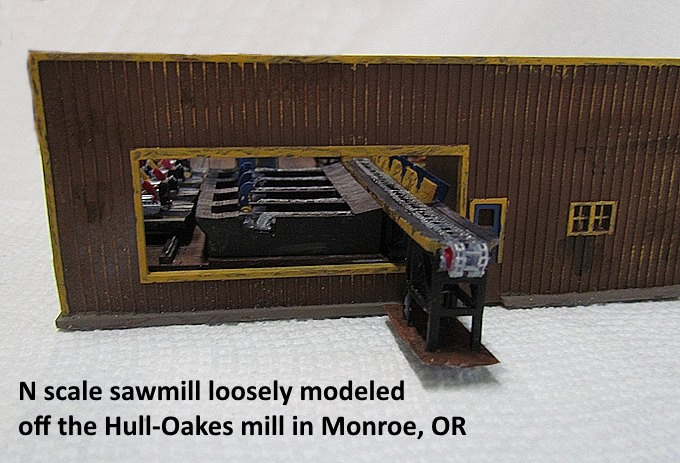
The logs travel from the mill pond to the mill on 4 different chains. There is a log lift that lifts the log out of the mill pond to the first chain and then moves the log to a chain going into the debarker building. There a chain moves the log into the debarker which obviously removes the bark as the log goes through it. On the other side of the debarker a chain moves the log along to the chain show above which moves it into the mill. At the end of that chain….
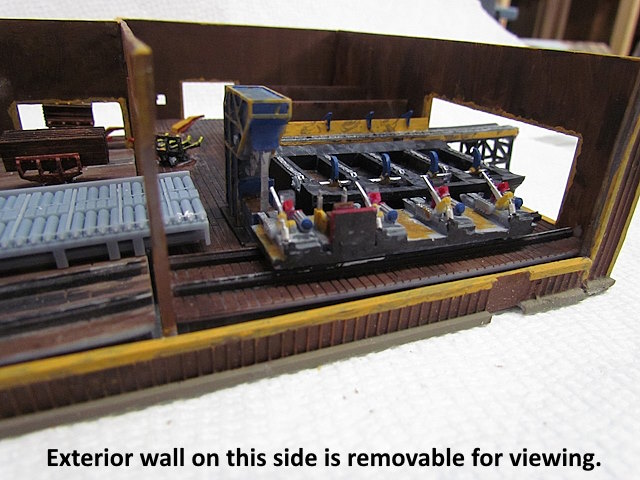
…. there are some paws (blue and visible in the back of the image above) that push the log onto the transfer table. There can be numerous logs on the table. The table has a mechanism that moves only one log at a time onto the log carriage. The carriage holds the log while the carriage passes the bandsaw and cuts a slab off. The the carriage moves the log towards the band saw for the next cut. The log can also be rotated 90 degrees at a time on the carriage to make additional cuts for either a large timber or to be cut into dimensional lumber.

Above one can see how the lumber that needs to be re-cut can move in by the re-cut saw. The next load on the dock is air dried lumber that will come in and be run through the planer (machine closest to the wall).
In the foreground when a slab is cut off the log by the bandsaw (barely visible on the right) the slab falls on the nearest set of rollers. It it is shot enough it moves over to the next set of rollers via the chain and the slab moves through the edger saw which cuts the rough edges off the slab creating a board of the width the edger is set for (different for different width slabs).
If the slab is too long to move over it moves down the rollers some and a chain saw comes up out of the hole on this side of the edger saw and cuts the slab into a shorter length. The one piece moves over to the edger rollers and is cut. The other piece that was cut moves back up the rollers towards the band saw and it moves over to the edger rollers and is cut.
A long timber that wouldn’t go through the edger is moved off the carriage onto the first set of rollers and …
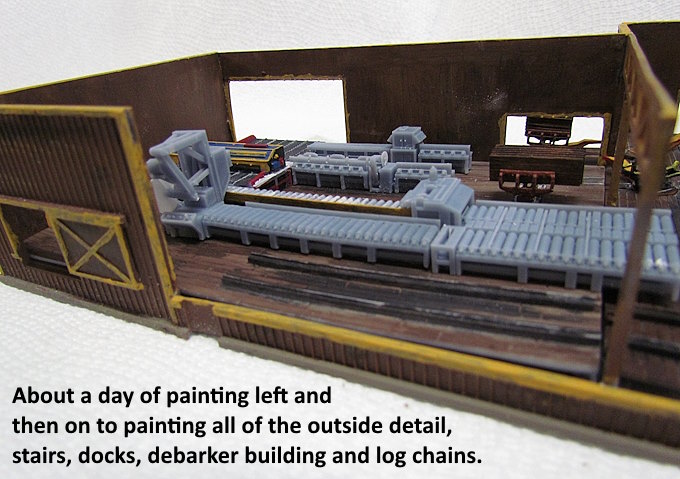
….. moves on down them to the large cutoff saw shown on the left end of those rollers. It is cut to length and moves out of the mill to be stored in the yard.
The boards that were cut by the edger move on down to the end of that set of rollers. There chains move the board over onto a table and another set of chains that move the board through the trim saw that can cut the board to different lengths. Those boards then move out to the green chain to be sorted.
They are also inspected and any that need to be re-cut to a shorter length due to a defect move back over to the dock where they are place on carts that take the to the re-cut saw. From the re-cut saw or the planner they are moved by conveyor belts back onto the chains after the trim saw and move back to the green chain for final sorting.
That is the workflow for this mill others are probably somewhat similar or might add a step or do and not follow all of those steps.
.... to be continued.
=========================================
A link to this whole build
( HERE ).
Sumner