I use three methods, depending on the usage.
(1) I use the standard slobber-the-feeder-to-the-side-of-the-rail if I'm not going to see it, or if it's in an area that won't be scenicked or photographed by me for "realism", such as in a hidden fiddle yard, tunnel interior, etc...which hides them.
Here's a photo of that method, which I'm sure everybody has seen before. 22 ga. feeder, code 55 Railcraft flex.

(2) I often solder feeders to my gapped PCB ties on my turnouts, such as at the frogs (for powered frogs), or on a short stock rail. The method is to flatten the end of my feeder with a flat-nose plier, then tin it, then bend it over at a 90deg. angle. Then I use a tiny drop of Supersafe Gel Flux (a non-acid, heat-neutralized flux...the BEST!!) apply that to the PCB tie, and solder the feeder to the PCB tie near the foot of the rail.
Here's a photo of a PCB tie feeder that's been painted prior to the last show to hide it. Code 40, hand-laid track, every fifth tie is a PCB.

(3) Method three is what I use mostly, which is to solder my 22 ga. solid-core feeders to the bottom of the foot of the rail. Unlike some modelers, I don't solder them before I lay my rail, but I wait until the rail is glued down. However, before the rail gets laid, I cut the spacers between two sets of ties away so that bare rail is exposed underneath, then I mark the cork roadbed with a Sharpie to tell me where I will solder the feeders later.
Although I can solder these feeders with a 30 watt iron, I use my resistance solderer, with tweezers (the points of which I have specially shaped to hold the feeder to the bottom of the rail foot), set to a very low setting so as not to vaporize Delrin ties and teeny Railcraft spikeheads.
Before you do this next step, make sure the solid-core wire you've chosen will slide easily into the 1/16" hole you drill. Test this on a scrap piece of wood. If not, then either get the next size up bit, or try to find wire that has thinner insulation.
I drill a 1/16" hole between my ties and directly adjacent to the foot of the rail. Be careful to not get too close with your drill-bit, because it will cut a semicircle out of the nickel silver foot if it's too close. Drill completely through both roadbed and subroadbed. If those two things are too thick for a "standard" length bit, longer ones are readily available at your local tool and equipment store (not Lowes or Home Depot). I bought two longer bits "just in case", and ended up using them a few times.
Strip about 3/8" from at least one end of your feeder. If you're going to construct a solder joint at the under-the-benchwork end, then strip the same amount away now too. I used 3M IDC's (red) so I only stripped the top of the feeder.
Flatten about 1/8" of the feeder with a flat-nose plier. You want a smooth, flattened end, so don't buy a plier with "teeth" unless they're really, really small.
Bend the flattened end to a little less than 90 deg. angle, since the hole you've drilled is not directly under the rail.
Tin the top of the bent feeder with a slightly generous amount of solder, so that it forms a small dome of solder. "Small" is the operative word here.
Put a few small kinks into the the feeder so it won't fall through the hole you've drilled in your roadbed/subroadbed, and insert it into the hole, so the bent portion is located under the foot of the rail, centered between two ties.
With a toothpick that has a drop of Supersafe Gel Flux on it, wet the feeder so capillary action wets both the bottom of the rail and the solder "bubble" on top of the feeder.
Hold the feeder against the bottom of the rail with an Xacto knife with a sharp #11 blade, and touch both the feeder and the base of your rail simultaneously. It will smoke, the solder will become instantly shiny and adhere to the foot of the rail...REMOVE YOUR IRON INSTANTLY AT THIS POINT...or you will melt ties, which you don't want to do.
Needless to say, your iron must be hot, with a clean, tinned tip. I use an old Archer (Radio Shack) 30W iron, and it works great.
Test the joint with your multi-meter, and give it a little pull from underneath. If it's a bad joint, it'll come loose, but don't pull too hard!
To make sure these under-rail joints retain their integrity, I put a couple of drops of thick, gap-filling CA on the feeder and wood surrounding it as it exits the hole underneath my subroadbed, and squirt Accelerator on each feeder glue job, then heat-cure it with a hair drier set on "high".
Here's a photo of a "virgin" under-rail-foot-feeder, which means it was done before painting, weathering and ballast...like it SHOULD be done!

Here's a photo of a "virgin" under-rail-foot-feeder after the rail has been painted. As you can see, it's starting to disappear.
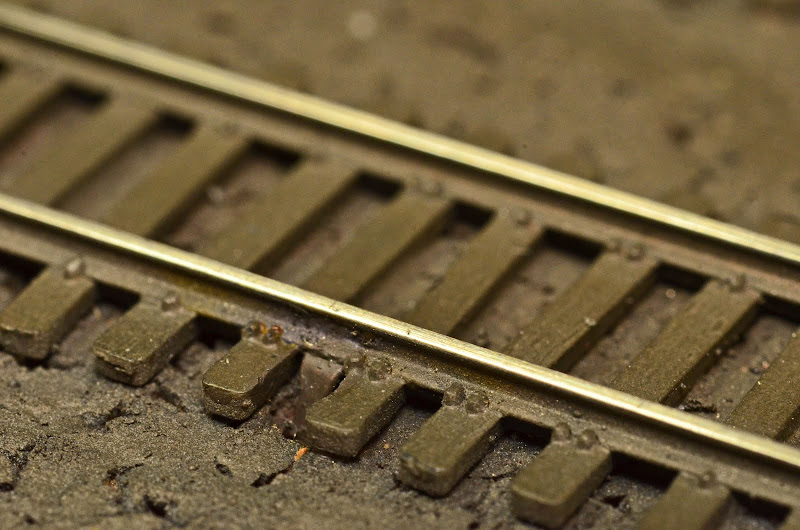
Every now and then, you might have to install under-rail-foot-feeders on track that's already painted, weathered and ballasted...which is a royal pain in the butt let me tell you! Unfortunately, about 1/3 of all my feeders were this type because I was converting over to DCC from DC and wanted each piece of rail to have its own feeder.
The main trick is buy a cheap "hot-knife" from Harbor Freight Tool (about 12 bucks if I remember correctly) and grind a #11 blade so that you can precisely melt/cut any under-rail Delrin spacer away without mistakenly lifting up the glued/ballasted/painted flextrack.
Do this after you scrape away the ballast from between the ties you've chosen to solder the feeders under. Also, scrape the paint away from the sides of the rail at your solder joint so it doesn't act as an insulator and make you melt ties.
Here's a photo of feeders installed after my track was painted, weathered and ballasted. The joint has been painted, but new ballast has not yet been installed.

Hope my experience assists anyone who has been hesitant to do it this way.
Cheers!
Bob Gilmore